PVDC (Polyvinylidene Chloride) coating is a versatile and specialized treatment applied to films and other substrates to enhance their performance and properties. PVDC coating significantly impacts the barrier properties, mechanical strength, and chemical resistance of the film. In this article, we will explore how PVDC coating affects the properties of film and its common uses in various industries.
Effects of PVDC Coating on Film Properties:
Barrier Properties:
PVDC is well-known for its exceptional barrier properties against gases, vapors, and liquids. When applied as a coating on films, PVDC creates a tight, impermeable barrier that prevents the passage of oxygen, moisture, and other volatile substances. This high barrier performance helps to preserve the freshness and shelf life of food products, pharmaceuticals, and sensitive electronic components.
Moisture Resistance:
PVDC-coated films exhibit excellent resistance to moisture and humidity. The coating prevents water vapor from penetrating the film, making it an ideal choice for packaging applications where moisture protection is crucial.
Chemical Resistance:
PVDC coating enhances the film's chemical resistance, making it resistant to many acids, alkalis, and solvents. This property is especially beneficial in applications where the film may come into contact with aggressive chemicals or corrosive substances.
Thermal Stability:
PVDC-coated films offer enhanced thermal stability, allowing them to withstand high temperatures without losing their barrier properties or mechanical strength. This property is particularly important for applications involving high-temperature processing or sterilization.
Flexibility and Strength:
PVDC coating imparts flexibility and strength to the film, enhancing its mechanical properties and making it more resistant to tearing and puncturing. This added strength ensures the film can withstand handling, transportation, and various packaging processes.
Transparency:
PVDC-coated films can retain excellent clarity and transparency, allowing for easy visibility of the packaged product. This feature is particularly important in food packaging, where consumers often prefer to see the contents before making a purchase decision.
Sealability:
PVDC coating improves the sealability of the film, making it easy to form secure and airtight seals during packaging operations. The improved seal strength ensures the contents remain well-protected and free from contamination.
Common Uses of PVDC-Coated Films:
Food Packaging:
PVDC-coated films are widely used in food packaging due to their excellent barrier properties and moisture resistance. They are commonly used for packaging snacks, baked goods, confectioneries, coffee, cheese, and other perishable food items. PVDC-coated films help extend the shelf life of food products by preventing oxygen and moisture from reaching the contents, thereby preserving their freshness and flavor.
Pharmaceutical Packaging:
In the pharmaceutical industry, PVDC-coated films are used for blister packaging of tablets, capsules, and other solid dosage forms. The high barrier properties of PVDC help protect the medications from environmental factors such as humidity and oxygen, ensuring their stability and efficacy throughout their shelf life.
Medical Devices and Sterile Packaging:
PVDC-coated films find applications in medical device packaging and sterile packaging. The barrier properties of PVDC help maintain the sterility of medical devices and protect them from contamination during transportation and storage.
Electronics Packaging:
PVDC-coated films are used in electronics packaging to protect sensitive electronic components from moisture and environmental damage. The high barrier performance of PVDC helps safeguard electronic devices during storage and transit.
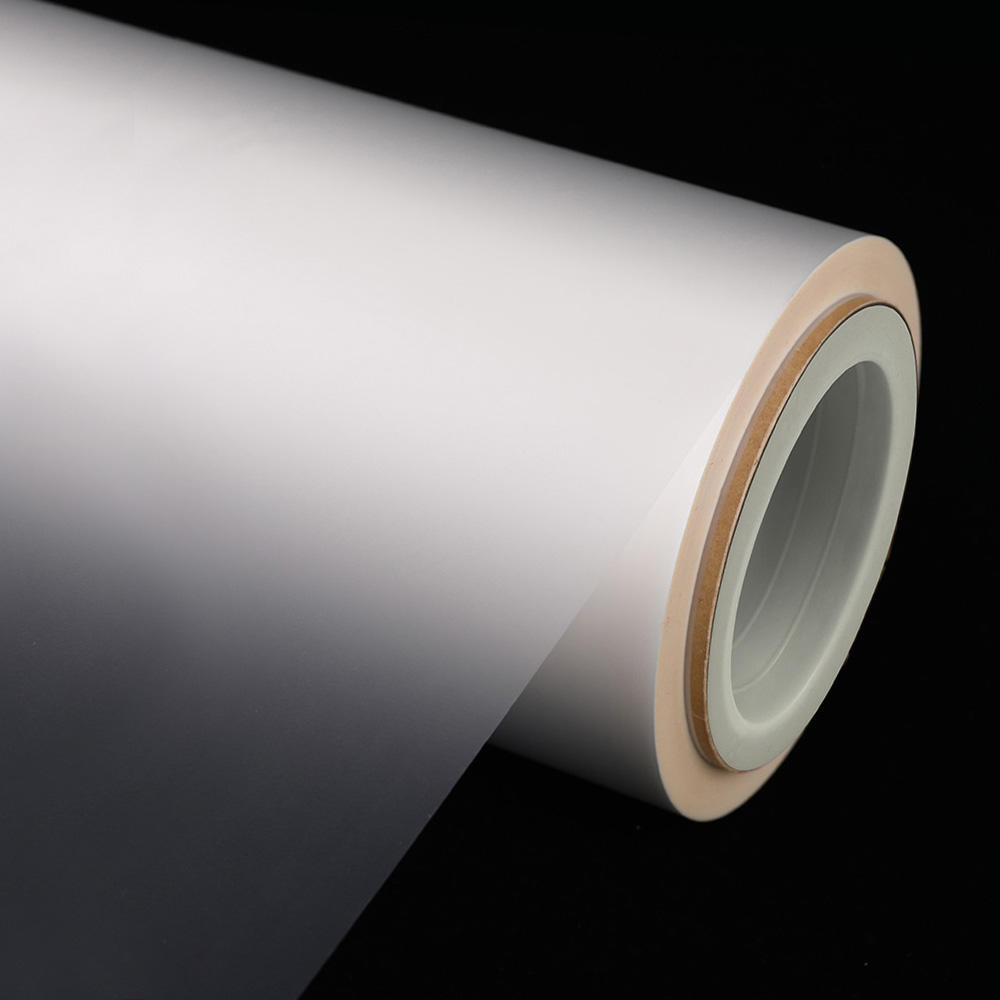
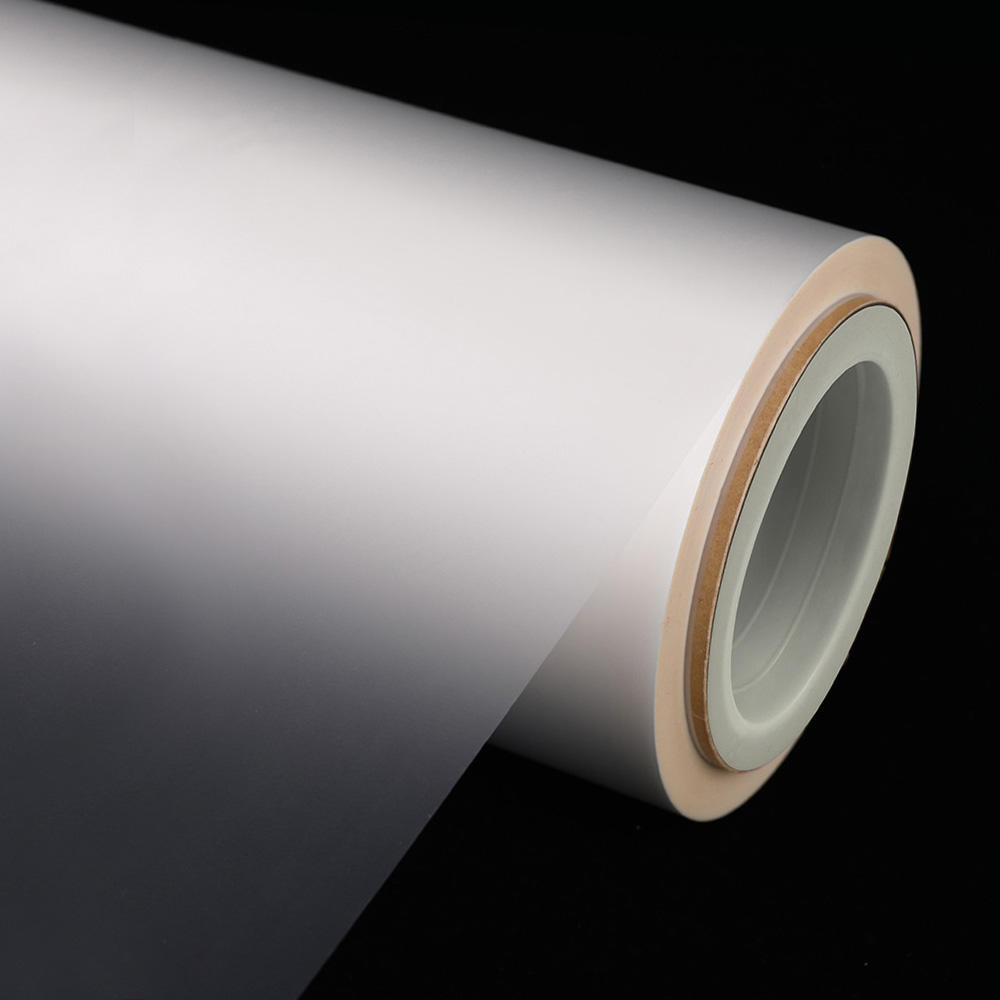
Agricultural and Horticultural Applications:
PVDC-coated films are used in agricultural and horticultural applications such as greenhouse covers and mulching films. The films provide protection against pests, weeds, and harsh weather conditions, while also maintaining an optimal microclimate for plant growth.
Industrial Packaging:
PVDC-coated films are used in various industrial packaging applications, including chemical packaging and packaging of corrosive substances. The chemical resistance of PVDC makes it suitable for packaging materials that need protection from aggressive chemicals.
Laminates and Flexible Packaging:
PVDC-coated films are often used as a component in laminates and flexible packaging structures. When combined with other materials, PVDC-coated films can provide enhanced barrier properties and sealability for various packaging applications.
Thermoforming:
PVDC-coated films are used in thermoforming processes to create rigid packaging containers for various products. The barrier properties and flexibility of PVDC make it suitable for forming packages with high impact resistance and barrier protection.
PVDC coating significantly enhances the properties of films, including barrier performance, mechanical strength, chemical resistance, and thermal stability. PVDC-coated films find widespread use in food packaging, pharmaceutical packaging, medical devices, electronics, agriculture, and various industrial applications. The ability of PVDC to create a robust and impermeable barrier makes it an ideal choice for protecting sensitive and perishable products from environmental factors. As technology and materials continue to advance, PVDC-coated films will likely remain an essential component in the packaging industry, ensuring the safe and efficient transport and storage of a wide range of products.